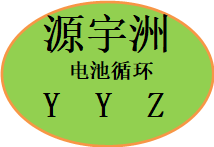
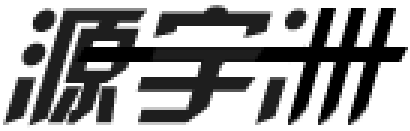

本文分享一个锂电池预充电排气工艺优化案例,首先简答介绍下电池样品信息:正极是NMC三元材料,负极是人造石墨,方形铝壳电池,设计容量约为20Ah。注液预充工艺为:
图1 电池工艺流程
具体工艺参数包括:
(1)一次注液:第一次注液,注液量为全部电解液的80%,注液机首先对电解液抽真空脱气泡,再对放置电池腔室抽真空,然后氮气加压注入电池内部,全自动分两次注入电解液。
(2)抽真空:注液完成后,对电池抽真空3min,让电解液充分浸润。
(3)常温静置:电解液继续浸润极片孔隙。
(4)开口预充电:充放电设备放置在环境露点-60℃的预充室,室内抽风机排风,另外不断补充干燥空气,此工段建设和后期运行费用非常昂贵。预充电程序为0.2C充电60min,SOC约20%。
(5)二次补注液:注入总电解液量的20%,再次抽真空2min。
(6)常压下,激光焊接注液口。
(7)化成:电池进行几次完整的充放电程序。
(8)老化,在4.0V荷电状态下45℃保存7天,再25℃保存2天,再分选。
预充电机理
在锂离子蓄电池首次充放电 (预充) 过程中,电解液在负极表面还原,不溶性的还原产物在负极材料表面沉积,形成一层钝化层,即固体电解质界面膜 (SEI) ,这层钝化膜具有固体电解质的特性,是电子的绝缘体却是Li+的优良导体,Li+可以自由的地通过钝化层嵌入和脱出。SEI 膜开始形成的电压并不是固定的,有可能是2 V,1 V或者0.8 V;而且,SEI膜在电池的充放电循环中会不断地形成,还与很多因素有关,例如,负极材料,电解液成分,添加剂,充电倍率,温度等。
方型电池内部残存气体对厚度有较大影响, 因此必须将预充产生的气体排出。预充排气方式一般有两种:一种方式是在预充过程中用胶纸、胶套棉花将注液孔贴住,负压封口时将气体一次排出;另一种方式是在预充过程中将注液孔敞开, 让气体自由排出, 此种方式对环境温湿度要求较高, 投资较大, 但工艺较为简单。
闭口工艺在封口时有一股较大的气流,会将电解液冲出,并且冲出的量不可控制。但开口工艺预充时气体缓慢排出, 不会带出电解液, 封口时也无电解液排出, 注液量一致性好。将电芯充至满电,解剖电芯后观察极片外观,发现:闭口工艺极片表面有很多斑迹, 开口工艺极片表面很干净,这是由于闭口工艺预充时电芯内部密布气泡,锂离子不能穿过气泡, 在负极片表面发生不均匀的电化学反应。开口工艺预充过程中,气泡被排出, 锂离子在负极片表面均匀反应,极片表面颜色表现出很好的一致性,SEI膜形成得较为致密。
为了提高锂离子电池的生产效率,需要优化电池预充电流和时间,从而在最短的时间内充分地将电池内的气体排出来。考察磷酸铁锂钢壳电池预充过程产气情况发现,随着预充反应的进行,自2.5V开始产气量迅速增加,到3.3V产气量达到最大值,之后出现消气现象。并选取在3.3V,3.65V,3.8V三个不同的预充电压对电池进行抽气封口,比较其倍率性能、高温荷电保持能力、循环及安全性能,结果表明3.3V时封口的电池具有最佳的性能。
下面,采用问题解决型QC-STORY八步骤回顾预充电排气工艺优化案例。
一、问题提出
在生产过程中,我们分析电池数据时发现容量、内阻一致性特别差。与预期值进行比较,容量比设计值20Ah约低2Ah,具体如图2所示。
图2 电池容量和内阻IR分布
二、现状调查与目标设定
首先对样品电池进行了多方调查,各工段数据分析。极片面密度满足品质管理要求,卷芯质量满足品质管理要求,电池质量满足管理要求,从这些数据分析可见,极片质量、注液量都满足要求,不是导致容量低的原因。
于是,我们拆解电池,发现极片与隔膜之间存在大量的气泡,如图3所示。对满电状态下的电池拆解观察,负极极片上存在很多没有反应的斑点(图4),气泡影响Li+在正负极来回往返,正、负极活性物质没有充分反应,容量偏低,而且一致性差。
图3 预充后电池拆解形貌
图4 满电状态下,负极极片形貌
这种气泡会导致负极表面不能形成良好的SEI膜,如果首次预充过程中形成的SEI膜不够稳定,随着循环的进行负极材料可能会剥落、破坏,在电极表面重新形成SEI膜,再次产生气体,降低电池的容量,加速电池的衰减。另外,充放电循环过程中,气泡影响Li+在正负极来回往返,正极活性物质也不能充分反应,降低可逆循环的效率。而且,这种气泡存在于电池壳体内,易引起电池的鼓胀、甚至爆炸的质量问题。
针对以上问题,我们成立了改善小组优化预充工艺,减少电池内部的气泡,消除负极极片上没有参与反应的斑点。并且最后确定了目标:容量达到20±1Ah,内阻0.95±0.20mΩ。
三、要因分析
针对以上出现的问题,我们从预充电原理出发,从人、机、物、法、环(4M1E)查找原因,并对具体的可能原因,提出了实验方案和实施计划。最终,我们分析主要的原因可能包括:
(1)目前的预充条件不合适,不能够使电池内部产气完全,预充不能达到理想效果;
(2)预充时电池内部产气完全,但是气体未能完全排出,仍存在极片与隔膜之间。
四、对策制定与实施
对于问题1:预充条件不合适,产气不完全。我们设计实验,通过改变充电时间调整预充电SOC状态,对比了不同SOC对产气的影响。
对电池预充电15min、30min、60min、90min,对应的SOC大约分别为 5%、10%、20%、30%。预充电之后,不抽真空拆解电池。电池拆解时,负极和隔膜粘结在一起不分开,依次展开电池正极、负极/隔膜,观察隔膜与负极之间留存的气泡,结果如图5所示。SOC达到30%时,气泡比SOC达到5%、10% 、20%时要少,但是仍旧存在很多气泡。
图5 不同SOC预充电电池拆解气泡情况
于是,电池预充电后再进行抽真空3min,再拆解电池观察气泡情况,结果如图6所示。同时还对预充电后抽真空3min的电池进行化成,然后在满电状态下进行拆解,观察负极极片形貌,结果如图7所示。电池在预充和抽真空3min后,拆解发现与图5不抽真空电池相比,气泡减少了一些。在不同的SOC条件下,电池内部气泡无明显差异。电池经过预充、抽真空3min及化成后满电拆解,发现SOC达到30%时黑色斑点量最少。再对比电池内阻,电池的预充SOC达到20%、30%时,预充后测得的电阻较小,而且SOC 30%时内阻最小,化成后容量高。
图6 不同SOC预充电再抽真空3min的电池拆解气泡情况
图7 不同SOC预充电-抽真空3min-化成满电电池拆解负极情况
因此,最终确定预充电SOC为30%。但是,气泡仍旧存在,我们再考察要因2的影响。
对于问题2:预充电产生的气体未能完全排出,仍存在极片与隔膜之间。我们调整了预充后抽真空的条件,主要包括时间和真空度。
首先,电池预充电SOC30%后,分别对电池抽取真空不同的时间,考察了抽真空时间对电池内阻IR的影响,数据结果如表1所示。通过实验可以看到,预充后抽真空6min,IR/OCV基本稳定,由于电池间还有一些微小差异,为了确保气泡充分排出,最终预充后抽真空的时间定确定为10min。
表1 不同的时间抽真空电池的IR变化
其次,考察了保持真空度的影响,之前抽真空工艺的真空度为-90kPa,我们设定更低的真空度到-96kPa,电池预充电SOC30%,不同真空度下抽真空10min,拆解观察气泡情况,结果如图8所示。实验结果发现,-96kPa真空度能够更好地排除电池极片内部的气泡,排气效果明显,而且负极极片表明更加平整,没有褶皱。
其次,考察了保持真空度的影响,之前抽真空工艺的真空度为-90kPa,我们设定更低的真空度到-96kPa,电池预充电SOC30%,不同真空度下抽真空10min,拆解观察气泡情况,结果如图8所示。实验结果发现,-96kPa真空度能够更好地排除电池极片内部的气泡,排气效果明显,而且负极极片表明更加平整,没有褶皱。
图8 不同真空度处理电池的拆解情况:左图-90kPa,右边-96kPa
五、效果检查与验证
通过以上改善实验,最终确定预充电排气工艺为:
预充电SOC约为30% (0.2C,1.5h),预充后抽真空10min,真空度 -96KPa。
确定工艺后,经过几个批次电池的试制,分析电池数据,容量为20.3±0.6Ah,内阻为0.87±0.05mΩ,达到设定目标。
图9 电池容量分布
六、标准化、总结与反思
预充电工艺优化实验结果经过多部门的确认,最后将优化的工艺参数写入工艺标准和作业流程书,标准化改善结果。
电池样品试制过程中,生产工艺存在很多需要进一步改善的地方,对于生产实践过程中的问题,首先采用三现二原(现场、现物、现实、原理、原则)主义,收集数据,把握现状,认识问题,此时,4M1E分析问题方法特别重要,各个工序的要素都是由人(man)、机械(machine)、原料(material)、方法(method)、环境(environment)这几个部分构成的,分析问题时就可以从这几个方面入手,采用特性要因图工具全面分析问题,找出重要的原因,并制定对策。
对策的实施,开始解决问题采用PDCA方法推进工作,对每次行动反复进行计划、实施、检查、处置的循环,明确的方法标准化,以SDCA方式进行维护活动。不断维护、改善推进工作。
而对于解决问题方法的评价则以QCDS作为标准,即除了品质之外,还要综合考虑成本、量和交期、以及安全。
总之,预充和化成是电池生产中的关键一步,直接决定SEI膜质量,从而对电池性能发挥和稳定性影响巨大。目前,为了提高锂电池的化成工艺效率和锂电池化成后的工作效率及容量和稳定性,发展了高温夹具化成。锂电池的化成过程中压力和温度两个因素起着决定性作用,高温对应疏松、更厚的SEI膜;低温对应致密、更薄的SEI膜。一般地,高倍率考虑高温,高容量考虑低温,或常温。高温可以降低电解液的黏度,加速离子的扩散,保证在大电流下,电子与离子迅速结合。压力确保电解液与极片的充分吸收和电芯厚度的均匀,压力可以保护电池界面的均匀性和平整性,有利于电子的均匀分布,同时对电池施加一定的压力,有利于缩短锂离子的扩散距离,在化成过程中不会因为涨气而影响电池的稳定性。